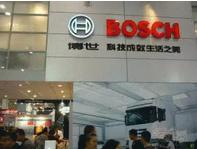
這家位于蘇州的工廠,是博世在歐洲以外最大的工廠,其最為知名的兩項產品當屬用于汽車ABS(防抱死剎車系統)和ESP(車身電子穩定系統)的電控單元,每年該工廠的生產量超過1200萬只。
12月10日,王波帶領著十多位記者到這座樣板工廠進行參觀。不久前,他剛完成工廠內ABS電控單元生產線的第一輪工業4.0改造。王波現在是汽車電子事業部生產體系規劃及工業4.0的部門經理,那是蘇州工廠今年2月剛設立的機構。
盡管這座博世于2004年投用的工廠自動化程度相當高,但仍有相當部分的工序需要人工參與。在ABS電控單元的生產線上,貼片機是頗為關鍵的一項設備。它負責在空白的集成電路板上裝配電容、電感等元器件,以實現ABS控制器的各項功能。貼片機可以全自動地完成元器件的裝配,但仍然需要人工向這些機器不間斷地補充電容、電感等物料,保證機器正常工作。
在一條ABS控制器生產線上,通常有四到五臺貼片機,每班配備有兩名操作工。他們負責設備巡檢,觀察這些機器所裝配的電容、電感等物料什么時候會消耗完,并提前向倉庫提出取貨要求。而倉庫的貨物配送到位后,操作工們還需要手動為貼片機補充成卷的電子元器件物料。這兩項工作分別占到操作工每天總工作量的30%和70%。
王波曾是負責這道工序的部門經理,他一直在考慮如何提高操作工們的工作效率。由于補料的操作手法需要相當技巧,暫時無法用工業機器人替代實現自動化。但巡檢貼片機這項工作,則可以通過工業4.0的方式進行改造。
其方法是:把生產線和物料倉庫這兩套以往獨立的系統連接起來,它們之間的信息溝通此前均由人工完成,比如貼片機的原料即將耗盡時,依靠操作工向倉庫管理系統反饋這一信息。而王波的設想,是在兩套系統間架起一座橋梁,將機器間的信息直接聯通。這也頗為符合工業4.0的理念,相比于工業3.0強調的自動化,工業4.0的重點在于實現機器間的信息互聯。
2014年初,蘇州工廠開始研發一套用于收集貼片機運行數據、并在需要補料時自動向倉庫發出指令的軟件,其被命名為自動叫料系統。去年6月,這套系統在工廠的一條ABS電控單元生產線上開始進行試驗。在系統運轉時,一旦貼片機的物料即將告罄,位于車間二樓的倉庫會自動得到指令,將物料通過電梯發往一樓,并由無人小車送往指定的生產線,操作工取貨后完成補料工序。
操作工也因此不再需要在生產線上例行巡檢。王波告訴界面新聞記者,在利用工業4.0改造后實施自主叫料系統后,24小時運轉的一條ABS電控單元表面貼裝生產線能節省20%的人力投入。同時,由于貼片機在何時需要多少物料有了更精確的預估數據,用于此的物料庫存也得以降低50%。今年年初,博世蘇州工廠的所有ABS電控單元生產線都開始采用自動叫料系統,并逐步向博世旗下的其他汽車電子生產線推廣。
在被任命為生產體系規劃及工業4.0部門經理后,王波也開始嘗試用更多工業4.0的理念改造工廠,比如在生產線的設備上加載傳感器,實時收集各類數據。根據這些傳感器所收集的機器運轉參數以及數據分析,判斷工廠內數量龐大的機器中,哪些會出現異常情況,從而針對性地預測性維修,以減少設備停工。而以往的方式,是目的性不強的定期巡檢或者等到機器故障后再進行維修。
盡管已經成為博世在中國的工業4.0樣板工廠,不過王波表示,就目前而言,工廠尚處于工業4.0的改造過程中。
在旗下工廠試點工業4.0,只是博世所計劃的第一步,成為服務供應商,向中國制造業企業批量輸出工業4.0,是它更為長遠的目標。當工業4.0這項理念越來越多地被中國業界所知曉和提及時,博世自然不希望錯過這片廣闊的潛在市場。正在蘇州工廠試點安裝的傳感器設備,預計明年就將面向對工業4.0有需求的制造業客戶銷售,其均由博世自行研發生產。
而與博世一樣,諸多來自德國的制造業巨頭們,正在持續地向中國輸出工業4.0——這項2013年由德國提出的概念。2015年10月,德國SAP與徐工集團簽約,共同開展工業4.0整體提升項目,該合作涉及的金額為5000萬元;西門子也在今年與遼寧省沈陽市及廣東省江門市簽約,就工業4.0展開合作。
關于工業4.0,曾有這樣一個說法:盡管100%的人聽說過工業4.0,但99%的人不知道它到底是什么。對于博世、西門子這樣的德國制造業巨頭而言,成為那1%中的佼佼者,毫無疑問是它們的目標所在。不過目前而言,工業4.0還并非完全成熟,它究竟能為工廠帶來多大程度的變化,也仍然處于探索階段。
轉載請注明出處。