近年來,得益于國家對新能源行業的鼓勵政策,我國新能源汽車及其相關行業的發展極為迅速。在各個新能源企業的不斷摸索進程中,大圓柱電池因其散熱性能優、內壓穩定、電芯一致性好、PACK工藝簡單、自動化程度高等優點從中脫穎而出。為了進一步減輕新能源汽車的重量,電池材質方面往往采用鋁、銅等材料制作。傳統的連接方式在焊接大圓柱電池過程中都有較為明顯的缺點,因此大圓柱電池的焊接成為了新能源發展途中的一個重大挑戰。在常溫下,大圓柱電池材料對1064波段的光束具有較低的吸收率。若激光功率密度較低,會造成較多的回返光,一方面使得焊接效果較差,另一方面大量的回返光會減少激光器的使用壽命。因此針對以上問題,銳科激光特研制出旗幟系列單模環形激光器RFL-1000/1000-SM-ABP-R,它可以高效完成新能源行業的圓柱電池的焊接任務。圖1 旗幟系列單模環形激光器RFL-1000/1000-SM-ABP-R銳科旗幟系列單模環形激光器是在環形光斑激光器基礎上進一步優化升級,中心光/環形光的芯徑進一步減小,從而得到更高的能量密度,在鋁材和銅材上進行焊接,具有更好的兼容性,且焊接效率高,一致性好,大幅提高成品率。相比于其他激光器,該系列單模環形激光器具有較多技術優勢:如圖3所示,相比于環形光斑激光器,旗幟系列單模環形激光器RFL-1000/1000-SM-ABP-R具有多項優勢:- 光束能量更為集中,對大圓柱電池的銅極具有更好的焊接效果。
- 光斑穿透能力更強,具有更大的深寬比,相同焊接條件下的焊接功率更小。
- 焊接熱影響區更小,更不容易破壞大圓柱電池的現有結構,能夠在更精準的焊接區域完成焊接任務。
- 可以產生更大、更穩定的匙孔,解決了匙孔不穩定的問題,使熔池內金屬蒸氣更容易逃逸,動能最小化。
大圓柱電池的焊接部位較多,如圖4所示。目前,動力電池的焊接具有諸多難點:- 個別待焊部位對光纖激光吸收率不高,焊接過程穩定性較差。激光焊接憑借能量密度高、熱影響區小、焊接精度高、焊接效率高、適應性強等優勢可以更好的完成圓柱電池的焊接任務。
而旗幟系列單模環形激光器RFL-1000/1000-SM-ABP-R基本可以勝任大圓柱電池中所有的焊接任務。且通過靈活可調的內外環光束,結合不同芯徑光束的優點,同時起到預熱、表面處理、改性、后處理的作用;并提高焊接質量,減小飛濺、炸孔、裂紋等缺陷,減少部件返工,良率可提高75%;大幅提升焊接效率;通過振鏡等外部設備,極大增加焊接速度,進一步提高大圓柱電池的成品效率。銳科旗幟系列單模環形光斑激光器在大圓柱電池的焊接案例
圖5為一種正集流盤的焊接效果,采用“sin波”的擺動方式可以得到更為美觀的焊縫,在增加焊縫數量的同時,使得焊接強度與背部殘留量也得以進一步的提高,總加工時間也僅為1.02s。而銳科旗幟系列單模環形激光器因其較小的芯徑,可得到更小的熱影響區,在正集流盤上繪制密度較大的焊接軌跡,也不會出現因焊縫重熔導致炸孔的現象。
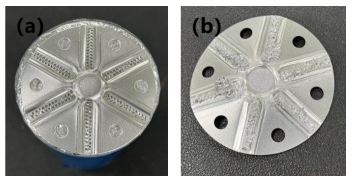
圖5正集流盤 (a)表面形貌(b)背面殘留
圖6為利用旗幟系列單模環形激光器RFL-1000/1000-SM-ABP-R焊接大圓柱電池負集流盤的效果,旗幟系列單模環形激光器的優勢使得整個焊接過程中并未出現飛濺、炸孔現象,且焊后負集流盤背面粘黏更多的銅極耳,相比于其他類型的激光器,具有更好的焊接效果,焊接時間也僅為1.854s左右。
旗幟系列單模環形激光器RFL-1000/1000-SM-ABP-R也能應用于防爆閥的焊接,如圖7所示。相比于大芯徑激光器,熔深熔寬難以精準控制,而采用單模環形激光器,熱輸入與熱影響區較小,能夠更容易得到合適的焊接效果,且焊接效率高,焊接時間為0.145s左右。
圖7防爆閥(a)表面形貌(b)微觀形貌(c)(d)截面形貌
底部穿透焊主要是將正集流盤與殼體進行焊接,待焊區域較小,而為滿足熔深要求,若采用大芯徑激光器需增加焊接功率,從而容易形成較大的熔寬,最終導致焊縫溢出待焊區域,導致工件變形。而采用旗幟系列單模環形激光器RFL-1000/1000-SM-ABP-R能夠得到較大的深寬比,輕松地在待焊區域完成焊接任務。單道的焊接時間為0.425s左右。圖8底部穿透焊(a)表面形貌(b)背面形貌(c)微觀形貌(d)截面形貌將旗幟系列單模環形激光器RFL-1000/1000-SM-ABP-R配合擺動焊接頭進行大圓柱電池封口的焊接,效果如圖9所示,單個焊接時間為2.33s,能夠得到較為美觀的封口效果,且焊接過程穩定,熔深較大,焊接強度高,一致性好。圖9 頂蓋(a)(b)表面形貌 (c)微觀形貌(d)截面形貌
通過以上焊接案例,可以看出旗幟系列單模環形激光器RFL-1000/1000-SM-ABP-R基本可以勝任大圓柱電池上絕大部分待焊區域的焊接任務,且焊接效果優勢明顯。也由此可以看出,在新能源領域,銳科系列單模環形激光器擁有得天獨厚的優勢。